随着智能手机的使用越来越广
、越来越方便
,其结构也更为复杂
,包括连接器,触摸屏
,金属壳和玻璃盖板,FPC柔性印刷线路板
、PCB主板
、摄像头
、电池
、上盖板
、天线
、底盖
,还有充电器
、耳机等
。
在纯手工生产线中
,手机主板生产车间的质量把控人员会拿起放大镜核查工人为高速贴片机所装载物料的准确性
,并对主板进行标记
。主板生产是除物料采购外
,生产手机环节的第一个步骤
。
接着
,待组装的手机屏幕
、手机的摄像头被安装到位
。随后工人开始测试手机的通话功能
、拍照功能等
,为手机充电并测试电池性能
。
各功能正常运行后
,扫描IMEI串号(国际移动设备标识)
,这是整个手机成品组装的最后一个环节
。手机在组装测试区检测合格后
,进入到包装环节
,工人把手机的附配件
、产品说明书等都包装好
,最后打包待检
。
■ 智能手机生产链的自动化现状
按照工艺来划分
,手机产业链可分成组装段
、核心部件段
、检测段
。
组装段包括点胶
、精密贴装
、预装
,还有精密压合
,锁螺丝
,这些自动化设备已基本实现量产
。
核心部件段包括SMT
、PSA
、激光切割
、打标
、焊接
,还有自动上下料
、抛光
、打磨
、精雕
、热弯等设备
,还有一段比较微小的模组如摄像头需要组装
。
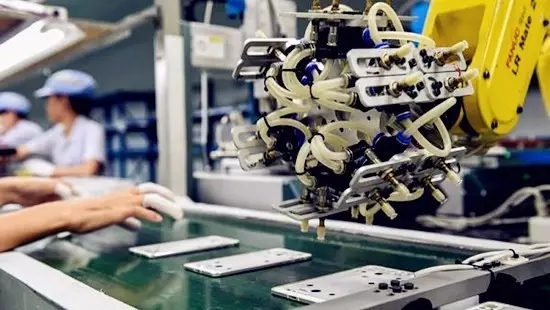
检测段
,包括尺寸量测
,如平面度
、段差
、间隙
,还有瑕疵检测
;也包括性能检测
,如射频
、音频
、MMI等
,这些性能可通过专门的仪表来检测
。
当手机各零组件被组合起来
,把手机背盖装扣上之后
,手机的组装就趋于完成了
。手机完成组装之后
,还要进行音频
、拍照
、GPS
、天线
、功能测试等特定项目检测
。
目前
,机器人可协助组装好的产品进行自动化检测
,检测内容包括音频
、拍照
、GPS
、天线
、功能测试等项目
,据手机厂商表示
,机器人检测的准确度可达到98%
。此外
,检测过程中移动手机
、定位检测等固定动作也可由机器人取代
,每个生产区域至少可减少20个人力
。
在整机测试环节
,采用机械臂
、大型自动化检测仪
、AOI自动光学检测仪等
,通过人机界面可对手机的SIM卡检测
、电池测试
、SD卡检测
、LED按键
、LCD测试
、LED背光等手机所有部件进行测试
。
总体来看
,SMT是自动化程度最高的流程
,也是目前最流行的电子组装技术
。首先是打印电路板(PCB)
,然后锡膏将处理器等芯片粘贴到PCB上
,回温固定
。透过电脑监控可以观察印刷电路板是否有瑕疵并标记
,等主机板全部打制完成后
,就会送到手机前期组装生产线进行产制
。目前整个流程可以实现全自动化
。
而人力密集区主要集中在整机组装环节
,包括组装
、测试
、包装等
,因为涉及焊接
、摆线
、合壳
、清洁显示屏
、贴镜片
、测试检测等
,以及辅料的上料和贴合等工艺
,自动化改造难度较大
,加上小批量多批次的生产特点
,对于自动化的柔性提出了更高的要求
。
相对而言
,后段的包装环节难度较小
,且已经有相对成熟的案例
,生产线上可配置自动封装机
,替代原本的手工封装
,可以实现整线的包装自动化
。
除了生产环节外
,工厂在运输环节内开始配备AGV
,斯坦德机器人合伙人王茂林分析
,AGV的价值就在于
,从原料仓到生产线
,再到成品仓中的物料运输
,对搬运的柔性化程度高
,需要不改变原有产线的前提下实现快速部署
,形成柔性生产线
,从而实现AGV替代“人”和“磁条车”
。
■ 手机产线自动化已成趋势
数据显示
,全球70%的电子产品在中国制造
,但在整个生产制程中
,仍有90%的工序以人工作业为主
,这意味着未来智能改造空间巨大
。
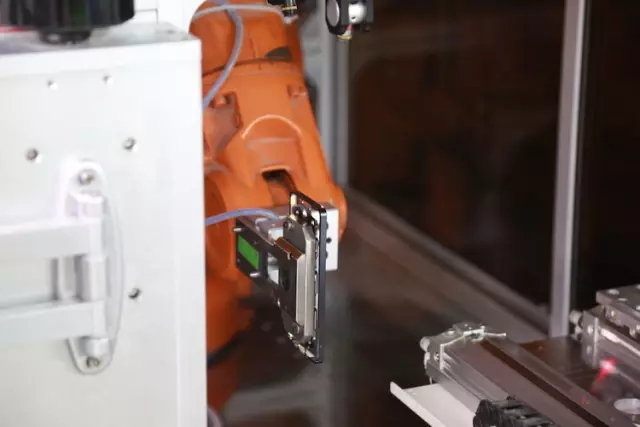
首先
,在前工序
,即壳料
、塑胶料
、金属料等处理方面
,如中框的CNC加工
,可采用抛光打磨工艺实现
。此外
,在卡槽
、HOME键的尺寸检测
,喷涂
,PCB板的组装和测试等工序
,可通过深入手机产业链的自动化集成商设计出自动化改造方案
。
其次
,在手机厂家或代工厂中
,组装和测试环节大概占据整个产业链80%劳动力流向
,“机器换人”既存在难点也蕴含着机会
。
库柏特机器人系统部总经理廖圣华介绍
,通过智能力控柔性装配解决方案和人机协作AI智能产线解决方案,采用AI视觉检测平台
,可运用于机器人无序上下料
、智能力控柔性装配
、机器人力控打磨
、智能缺陷检测
。
最后是后道包装环节
,成品通过MMI测试
、二维码写入之后
,就会进入包装
,装箱码垛等环节
,这也是国产工业机器人厂家应用较成熟的领域
。
据业内人士估计
,前工序
、组装
、测试和后道包装四大环节中
,前工序可能占从业人员10%
,装配占60%
,测试占20%
,包装占了10%
。按这个劳动力的分配
,从减员增效的角度看
,装配和测试的自动化升级改造空间较大
。
■ 手机自动化产线的新要求
目前来看
,手机厂商日益迫切的自动化需求与自动化厂商能力之间依然存在很大的矛盾
。
首先
,手机产品小批量
、多品种
,工艺复杂度高
,并要求节拍速度快
,因而需要高柔性产线以兼容其所有系列的产品
。
此外
,单型号产品生命周期越来越短
,OLED全面显示屏
、双曲面玻璃
、无线充电
、面部识别
、3D相机
、5G等新功能的更新换代则伴随着工艺的革新
。
第二
,需考虑到设备的折旧周期
,目前设备使用期限大概在3到5年
,而手机的生产周期相对较短
,大概为8-12个月
,因而对设备的可重复利用率要求高
。
第三
,对投资回报周期苛刻
,终端客户要求在一年半到两年就要能收回成本
。
从终端用户角度来看,中大型企业引入生产线主要考虑是否适应工业4.0的发展
,大厂商具有大额订单的支撑
,希望进行整线自动化的升级改造
,提高其市场竞争力
。
因此
,中大型终端企业需要内部+外部的配合协作
,硬件+软件的落地
,考验企业本身的可塑性与决断力
,因为需要投入大量资金
。
对中小微企业而言
,成本是其首先考虑的因素
,同时考虑投资回报期的问题
。目前
,中小企业以手工或半自动化为主
,更倾向于单工位的自动化替代
,由人工到半自动
、自动化的升级迭代
。
从系统集成商角度来看
,规模较大的集成商应从产线
、物流到系统进行整合
,加强软件的开发
、数据解读
、界面处理等方面的投入
,向数字化工厂方向发展
。
规模较小的集成商应在某个领域做精做专
,积极与机器人厂商做专业化
、定制化合作
,合作是较好的路径
。
从本体制造商角度来看
,针对3C行业的特点
,首先机器人需要能够适应柔性化生产
,快速完成产品生产的准备工作
,满足用户的差异化需求
;第二
,机器人需要高精度
、高速度
,或在某些指标上拥有“一技之长”
;第三
,机器人趋于小型化和轻量化
,节省空间的同时便于使用者在现有产品上进行改造
。
高工产研机器人研究所所长卢彰缘表示
,事实上
,应用方案及项目实施是制胜关键
,本体厂商与经销商
、集成商一道
,致力开发具体工艺段的应用方案
,打造标准工艺段应用的目标可以是可复制
、可靠性高
、导入迅速
、投资回报期小于1年
。
因此
,机器人本体厂商
、系统集成商需要与终端客户
、自动化企业客户真诚合作
,共同致力于开发手机智能产线
,让手机企业生产智能化
。
【转载】